業務用3Dプリンターに対するニーズの変化とは?最終製品や量産化も可能にする技術の進歩
2024/05/31

業務用3Dプリンターのニーズが大きく変化しています。かつては主に試作品やデザインの確認、オーダーメイド部品の製造に使われていましたが、最近では最終製品の製造にも利用されるようになっています。この変化の背景には、新たな造形技術の進化や3Dプリンターの価格低下があります。これにより、高品質かつ迅速に部品や製品を製造することが可能となり、企業は製造プロセスの効率化や柔軟な生産ラインの構築を目指すようになりました。
3Dプリンターのニーズが変化している!その理由は?
かつて、業務用3Dプリンターは試作品製作やデザインの確認、オーダーメイドの部品の作成などに主に活用されていました。近年ではそれだけにはとどまらず、最終製品の製造にも利用されるようになっています。
◇試作品から最終製品製造へ
近年、3Dプリンターは試作品製作に留まらず、最終製品の製造にも活用されるようになっています。RICOHのアンケート調査では、「最終製品への利用」が増加しており、2021年には前年比2倍以上の12%に達しました。
この動向の背景には、企業が形状やデザインの確認に加えて、効率的な製造プロセスや柔軟な生産ラインの構築を目指す傾向があります。3Dプリンターは、高品質かつ迅速に部品や製品を製造できるため、これらのニーズに応える理想的なツールとして注目されています。
◇最終製品製造に使用され始めた理由
最終製品での3Dプリンター活用が増えた主な理由は複数あります。まず、新たな造形技術の開発が挙げられます。最近では、熱溶解積層方式に加えてさまざまな造形方式が開発され、強度の高いフィラメントも登場しています。これにより、より多様な製品を製造できるようになりました。
また、3Dプリンターの価格が下がったことも大きな要因です。特許の切れにより安価な3Dプリンターが市場に登場し、製造業界でも導入が容易になりました。これにより、製品開発のコスト削減や柔軟性の向上が図られ、最終製品への活用が進んでいます。
最終製品製造や量産化における課題
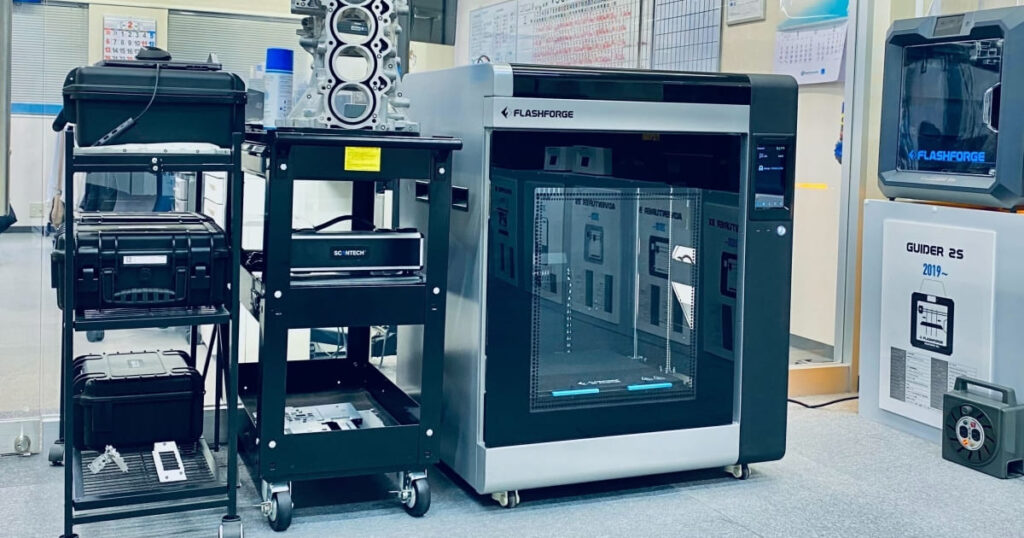
画像出典先:flashforge
最終製品製造や量産化における課題は多岐にわたります。製品の品質や信頼性を確保するための技術的な課題や、製造プロセスの効率化やコスト削減を図るための経済的な課題があります。特に、3Dプリンターの場合は素材コストや造形時間、設備投資といった面での課題が存在します。
◇造形スピード
3Dプリンターと金型での射出成形とでは、製品を作るスピードが大きく異なります。射出成形では、数10秒のサイクルタイムで多数の製品を同時に作ることができます。これに対して、3Dプリンターは層を積み重ねて製品を造形するため、一般的に数時間かかります。この違いは、射出成形が大量生産向きであるのに対し、3Dプリンターは少数生産や試作品制作向きであるという点にあります。
◇コスト
3Dプリンターの最終製品製造や量産化における課題のひとつは、コスト面です。3Dプリンターの素材コストは比較的高価であり、1kgあたり数千円と言われています。大口取引でも数百円程度となりますが、これは射出成形などの他の製造方法に比べて高額です。また、3Dプリンターの造形時間も数時間が一般的であり、これに比べると射出成形では数10秒のサイクルタイムで量産が可能です。そのため、3Dプリンターのコスト面での課題を克服することが重要です。
量産化可能な3Dプリンターを活用して課題を解決
量産化可能な3Dプリンターは、製造業界に革命をもたらす可能性を秘めています。従来の製造方法に比べ、柔軟性や効率性が向上し、低コストで短期間に製品を生産できます。このような3Dプリンターの活用により、様々な産業で課題解決が可能となります。
◇Creator4S
「Creator4S」は、最終製品づくりに適した3Dプリンターです。このプリンターは独立型デュアルエクストルーダーを採用しており、2本の出力ノズルを備えています。これにより、左右対称の造形や異なる素材の組み合わせなど、多彩な造形が可能です。さらに、同時に2つの造形物を出力することもできます。
また、Creator4Sは約20種類のフィラメントに対応しています。3種類のエクストルーダーを搭載しており、カーボンファイバーからスーパーエンプラまでの幅広いフィラメントを利用できます。さらに、ヒートチャンバーを搭載しており、装置温度を一定に保つことで、温度変化による反りや収縮を防ぎ、高精度な造形物を実現します。
◇Stratasys Origin One
「Stratasys Origin One™」は、ストラタシスの光造形方式の3Dプリンターであり、生産グレードの工業用3Dプリンターとして高速で高解像度な造形を実現します。従来の光造形方式の3Dプリンターと比較して、高い強度、衝撃耐性、弾性、耐候性を備え、従来の常識を覆す性能を持っています。
Origin Oneは、量産でも高精細な造形を可能にし、解像度が下がることなく超高精細な単体造形も実現します。従来のDLP方式に比べて4Kの解像度で造形することができ、これにより圧倒的な高精細さと量産性を両立させています。
最終製品の量産化に成功した国内事例を紹介
NITTOKUはCarbon社の3Dプリンターを導入し、年間10万点近くの最終部品の大量生産を実現し、主にRFID製品の製造に活用されています。一方、株式会社計測工業はFigure 4 Standaloneを導入し、自社開発製品の最終製品製作に3Dプリンターを活用しています。
◇NITTOKU株式会社
NITTOKUは、Carbon社の3Dプリンターを導入し、年間10万点近くの最終部品の大量生産を実現しています。主にRFID(非接触タグ)製品の製造に活用されており、ICチップとコイルから構成される非接触タグの製造に使用されています。
これにより、直径3mmの世界最小クラスの非接触タグなど、さまざまなサイズや形状のRFID製品を効率的に量産しています。
◇ 株式会社計測工業
Figure 4 Standaloneを導入した計測工業は、自社開発製品の最終製品製作に3Dプリンターを活用しています。これにより、開発リードタイムを25%短縮し、新領域における計測機器の開発にも挑戦しています。以前はすべての製作作業を外注していたが、3Dプリンターの導入により内製化が可能となり、製品の開発プロセスを効率化しました。
業務用3Dプリンターの需要が変化しており、以前は主に試作品やデザインの確認、オーダーメイド部品の製造に使われていましたが、最近では最終製品の製造にも利用されるようになっています。
この変化の背景には、企業が形状やデザインの確認だけでなく、製造プロセスの効率化や柔軟な生産ラインの構築を求める傾向があり、3Dプリンターがこれらのニーズに応える理想的なツールとして注目されています。最終製品での3Dプリンター活用が増えた理由は、新たな造形技術の発展や3Dプリンターの価格低下などが挙げられます。
しかし、最終製品製造や量産化には課題もあり、特に素材コストや造形時間、設備投資といった面での課題が存在します。量産化可能な3Dプリンターの活用により、従来の製造方法に比べて柔軟性や効率性が向上し、低コストで短期間に製品を生産できる可能性があります。
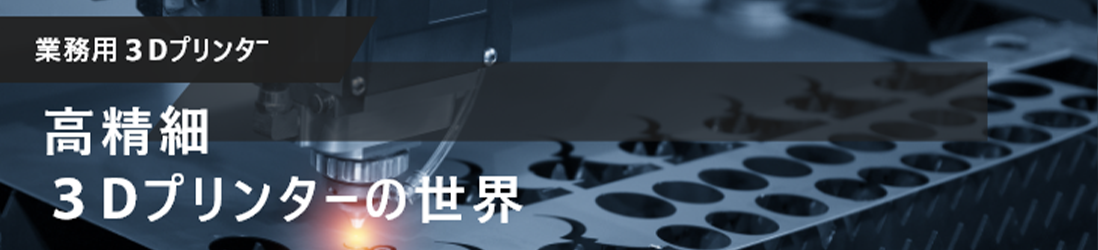