3Dプリンターで微細な部品の試作に成功!
2024/06/27
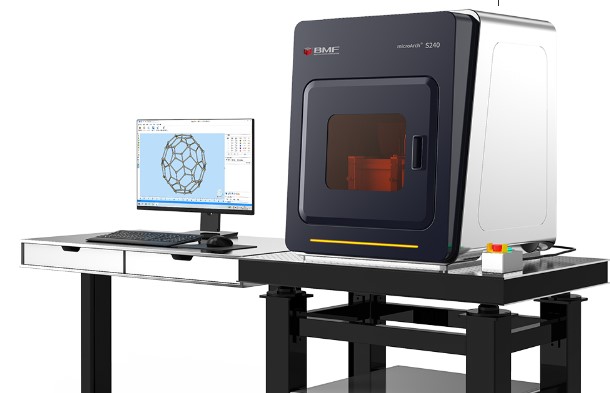
あるコネクターメーカーは、試作品の制作に1か月以上もかかる課題に直面していました。設計の確認や改善が難しく、製品の性能や使い勝手に不安が残りました。
業務用3Dプリンターの導入を検討し、高精度かつ極小サイズに対応できるBMFのmicroArch S140を選定します。結果として、試作品のリードタイムが数日に短縮され、開発スピードと効率が大幅に向上しました。
試作のリードタイムを短縮したい!
あるコネクターメーカーは、試作品の制作に1か月以上もかかるという課題に直面していました。設計者が図面や頭の中でイメージを進めるだけでは、実際の形状や機能性を確かめることが難しく、製品の性能や使い勝手に不安が残ります。
そのため、製品の試作を早期に行い、設計の確認や改善を容易にするために、業務用3Dプリンターの導入を検討していました。
◇多様な試作への対応
企業が多様な試作に迅速に対応するためには、製品の規格や性能の急速な進化に迅速に対応する必要があります。特に、スマートフォンや車載機器など、幅広い電子機器向けにコネクタを製造している企業では、この課題が特に顕著です。
このような状況に対応するためには、迅速かつ効率的に多様な試作に対応することが不可欠です。これにより、製品開発サイクルを効果的かつスムーズに進めることが可能となります。
◇リードタイム短縮
業界によって要求されるコネクタの仕様も異なるため、設計段階での確認が欠かせませんが、試作のリードタイム短縮が大きな課題です。試作型を起こして試作部品を作ることで機能面を確認していますが、1か月程度の時間がかかってしまいます。
試作には、設計者が頭や図面の中で設計を進め、実際に形を見て触れることで機能性や使い勝手を確かめることが不可欠です。そのため、試作のリードタイムの短縮が欠かせない問題点となっています。
3Dプリンター選定における課題
最初はFDM方式の3Dプリンターを検討していましたが、細かい部分まで対応できる機種が見つからず、また、同時に複数のアイテムをプリントすることも困難でした。
導入の決め手は、「不可能が可能になった」と感じたため、BMF方式の3Dプリンターを導入しています。
◇FDM方式では精度が不十分
FDM方式は、3Dプリンターの主流な造形方式のひとつで、熱可塑性樹脂を使った材料を溶かし、積層して造形物を作ります。この方式では造形物の表面に凹凸が目立ちやすく、また積層方向の強度が低いという課題があります。
これに対して、液槽光重合方式(SLA)は光硬化性樹脂を使用し、UVライトで硬化させることで高精度かつ滑らかな造形物を作ることが可能です。しかし、洗浄やサポート材料の取り外しなど、後工程の手間がかかることが欠点です。
FDM方式は手軽に扱える反面、精度や強度に課題があり、SLA方式は高精度で美しい造形物が作れますが、後工程に手間がかかることが挙げられます。どちらの方式も特徴や適用範囲が異なるため、用途に合わせて選定することが重要です。
◇同時プリントが難しい
光造形方式(SLA)のDLPやLCD方式は、Z軸全体を同時に硬化させるため、比較的短い時間で複数のアイテムをプリントできます。一方、熱溶解方式(FDM)やレーザータイプの光造形方式は、1本の筆で平面を描画するため、同時プリントには適していません。
同時に複数のアイテムをプリントしたい場合は、モデル形状や設定パラメーターによって異なりますが、光造形(SLA)のDLPやLCD方式を選択することが効果的です。
BMFのmicroArch S140を導入
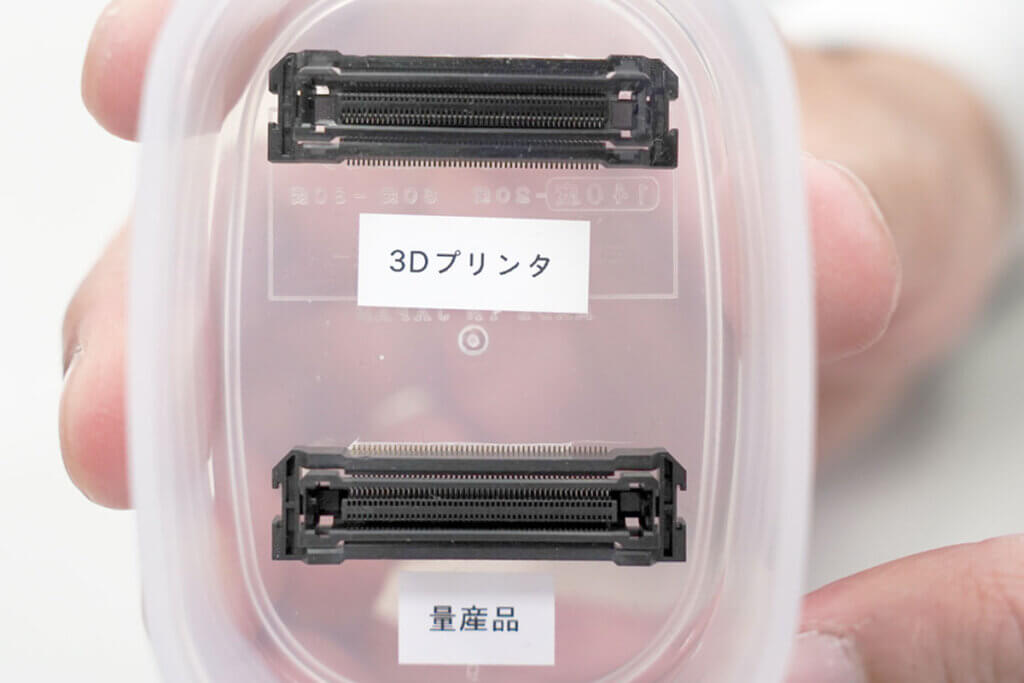
BMF JapanのmicroArch S140は、世界最高水準の精密さを実現しつつ、実用的なサイズと速度を維持しています。これにより、今まで不可能とされていた微細な部品や構造の製造が可能になりました。
◇microArch S140とは
microArch S140は、独自のマイクロナノ光造形を採用した機種です。10μmという精密光学解像度を持ち、超微細構造であっても高精度で造形できます。造形材料では樹脂材料だけでなく、セラミック材用にも対応が可能です。
また、マイクロスケールの造形能力を持ちながら、造形時間は実用的な範囲内であるため、試作品の開発での待ち時間を減らせます。さらに、3D編集に特化したMagicsスライスソフトウェアが標準装備されているため、出力までの工程を効率化できます。
◇極小コネクタの造形が可能に
世界最高水準の精密さと実用的な速度を保ちながら、数mm~数cmといった極小サイズの出力が可能です。そのため緻密かつ正確な再現性を求められる医療器具、マイクロ流路、MEMS、バイオ・製薬、エレクトロニクス、教育、研究開発など、幅広い業界で部品製造に最適です。
コネクターメーカーが扱う極小パーツの造形ができる点が、今回の導入において大きな決め手となりました。
試作の検証が数日で完了できた
microArch S140を導入したコネクターメーカーでは、製品開発のスピードが大幅に向上し、効率的な開発体制を整えることに成功しています。
◇試作品でも機能性の検証を行えた
3Dプリンターで作成した試作品を用いることで、試作段階でも機能性の検証が可能になりました。
高い精度で出力されたため、コネクタのボタンを押しながら端子を接続する、金属部品と樹脂部品を組み合わせて、実際に接続した際の機能を確かめるといった検証が、試作品であっても行えたのです。
コネクタは外す際にボタンを押す構造であり、こうした機能性の検証に試作品が役立ちました。
◇開発スピードが向上した
試作の製造から検証までに約1か月かかっていた工程が、3Dプリンターの導入により数日に短縮されました。
これまで簡易型を作成し、手での嵌合を確認するために長期間を費やしていましたが、3Dプリンターを活用することで同様の検証を短期間で行えるようになったためです。また、シミュレーションでは難しい部分を実際に試作して確認できる点も、開発を促進させました。 開発スピードが確実に向上し、コストやリードタイムの削減にも繋がっています。結果として、開発の効率が大幅に改善しています。
あるコネクターメーカーは、試作品の制作に1か月以上もかかるという課題に直面しました。設計者が図面や頭の中でイメージを進めるだけでは、実際の形状や機能性を確かめることが難しく、製品の性能や使い勝手に不安が残りました。そのため、製品の試作を早期に行い、設計の確認や改善を容易にするために、業務用3Dプリンターの導入を検討していました。
特に、スマートフォンや車載機器など、多岐にわたる電子機器向けにコネクタを製造する企業では、製品の規格や性能の急速な進化に迅速に対応する必要があります。このような状況に対応するためには、迅速かつ効率的に多様な試作に対応することが不可欠でした。
最初はFDM方式の3Dプリンターを検討しましたが、精度や同時プリントの難しさが課題でした。しかし、BMFのmicroArch S140を導入することで、「不可能が可能になった」と感じ、試作品の製造から検証までのリードタイムを数日に短縮できました。この3Dプリンターの導入により、製品開発のスピードと効率が大幅に向上し、設計段階での確認や改善が容易になりました。
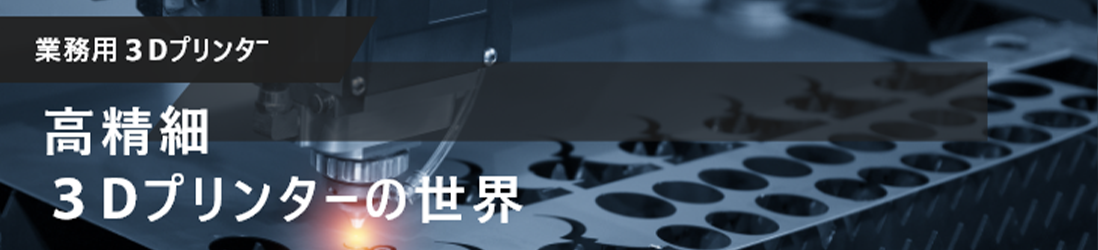