3Dプリンターで造形した部品は水中で使える?
2024/08/26
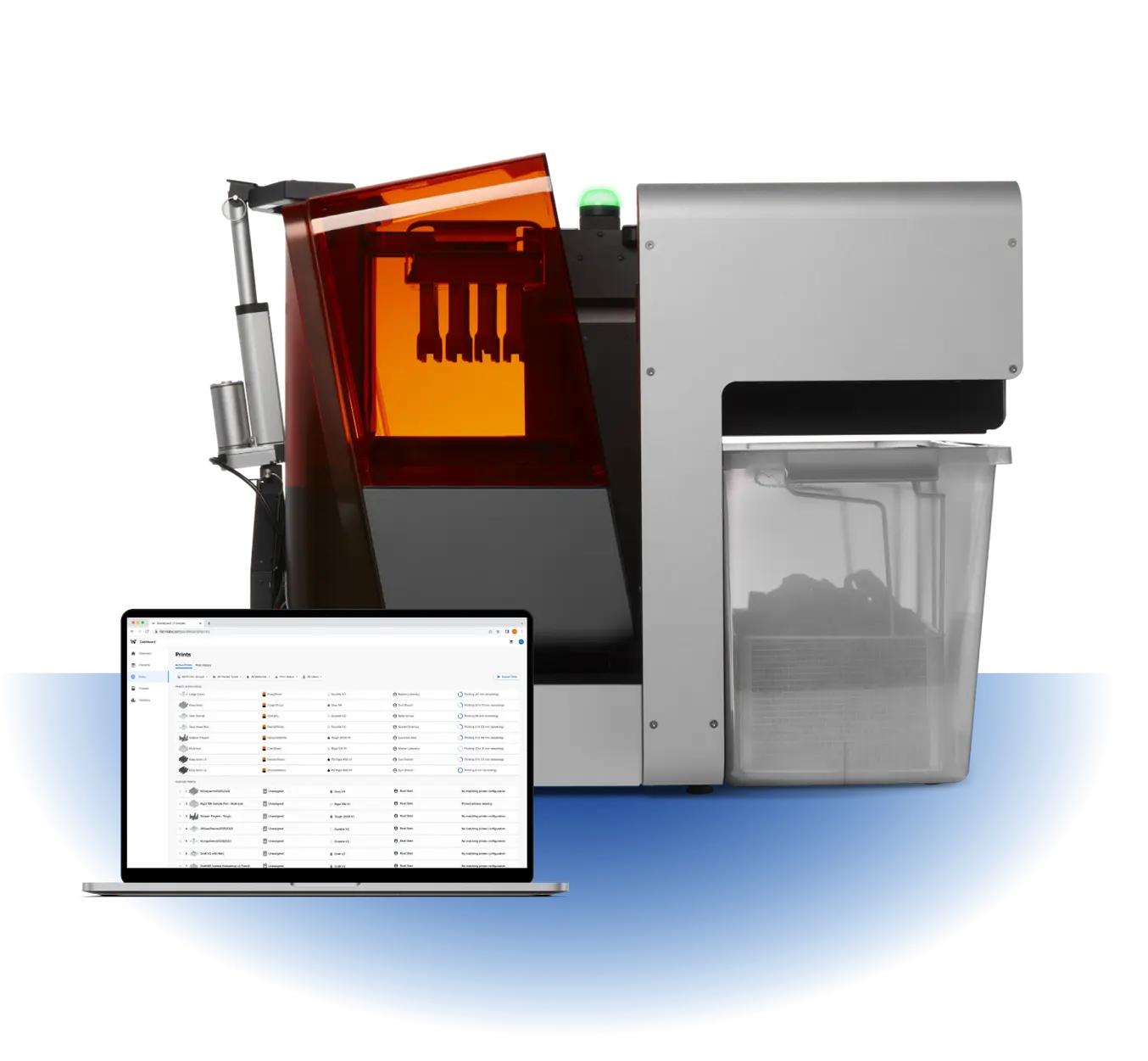
3Dプリンターでの造形は方式により気密性が異なり、SLA方式やMJ方式が最も高い気密性を持つため、特に水中で使用される部品の製作に適しています。しかし、高い耐久性と耐水性・防水性の確保が必要なうえに、部品が高い圧力に耐えられるよう、適切な材料選定や造形方法を求められます。
R大学の研究チームはSLA方式とエポキシ樹脂を組み合わせ、深海の圧力に耐えるカメラ筐体の製作に成功しました。使用した3DプリンターはformlabsのForm 3Lで、優れた精度とスピードが特徴です。成功を受けて、同チームは光ファイバーケーブルの器具や人工呼吸器の部品も製作し、研究の進展に寄与しています。
造形方式によって気密性は異なる
3Dプリンターは、3D-CADや3DCGのデータをもとに、一層ずつ材料を積み重ねて造形しますが、造形方式は複数あります。採用する造形方式によって気密性が異なり、気密性はFDM方式、SLS方式、SLA方式・MJ方式の順で高くなります。
◇FDM方式
FDM(熱溶解積層)方式は、加熱して溶融した熱可塑性樹脂をノズルから押し出し、層ごとに積層して造形する方法です。幅広い材料に対応しており、対応する設備も多く販売されているため、広く普及しています。
FDM方式では、リール状の樹脂を溶かしながら一層ずつ積層していく過程で、微小な隙間が発生することがあります。条件を変更することで隙間を小さくできますが、完全に排除することは難しく、十分な気密性が確保できないことも少なくありません。
◇SLS方式
SLS(選択的レーザー焼結)方式は、粉末焼結積層造形法やレーザー焼結法とも呼ばれ、粉末床溶融結合法のなかで代表的な造形方式です。熱硬化性樹脂などの粉末材料をプラットフォームに敷き詰め、設計情報に基づいて赤外線レーザーを用いて硬化させたい部分だけを焼結します。
溶融時に粉末の隙間にも樹脂が埋まり、内部の密度は99%以上に達します。小さな隙間が残ることもありますが、3㎜以上の厚みにすれば気密性を十分に確保できると考えられています。
◇SLA方式・MJ方式
液体樹脂に紫外線を照射して硬化させる方法です。液体樹脂を使用するため、造形時に内部に気泡が含まれにくく、ほぼ100%に近い密度で造形することが可能です。SLA方式・MJ方式の3Dプリンターを使えば、気密性に優れた造形物を作れます。
水中で使う部品の課題
海外のR大学の研究チームは、3Dプリンターで深海カメラ筐体を製作しようと考えていました。海中でカメラを使用すると圧力がかかり、積層の僅かな隙間から海水が入ってくる可能性があるため、製作時には高い耐久性と耐水性・防水性を確保することが課題となります。
◇耐久性
1気圧は、1 cm²あたり1kgの圧力です。水深10mごとに、1気圧ずつ圧力し、海面には既に1気圧がかかっているため、水深6,500mでは約651気圧の計算になります。651気圧とは、1 cm²に約651kgの圧力がかかるということです。
深海カメラを海に沈めると、この圧力により映像が影響されます。そこで必要となるのが深海カメラ筐体ですが、当然のことながら深海カメラの筐体も圧力の影響を受けるため、作る際は高い耐久性が求められます。
◇耐水性・防水性
どの造形方法を採用しても、3Dプリンターの造形物には目に見えない積層の隙間が存在し、そこから海水が入ってくる可能性があります。深海カメラ筐体に水が入ると、カメラ本体の故障につながるため、深海カメラ筐体には高い耐水性と防水性も必要です。
造形物の耐水性・防水性は、3Dプリンターの種類、素材、造形物の厚みなどによって左右されます。そのため、深海カメラの筐体を作る際は、適切な製作プランを立てることが重要です。
含浸処理を行って隙間を塞ぎ、その後に塗装を施すことで防水性を向上できますが、使用する環境によっては100%の防水性を実現することは難しいとも留意しておく必要があります。
formlabsのForm 3Lで深海カメラ筐体を造形
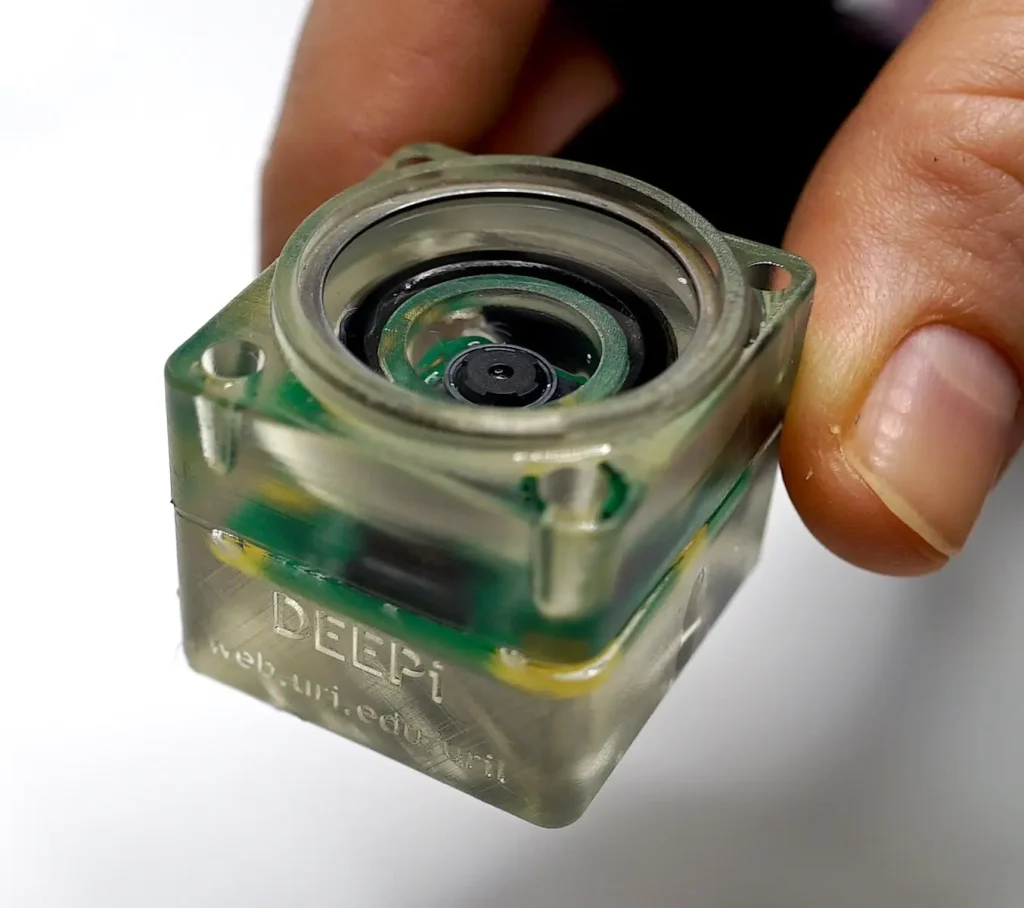
3Dプリンターの造形物は多孔質であり、加圧環境には適さないというのが一般的な認識です。そこでR大学の研究チームは、SLA方式3Dプリンターとエポキシ樹脂を採用することにしました。SLA方式の機能性と、耐久性と耐水性に優れたエポキシ樹脂の特性を組み合わせることで、海底の圧力に耐えられる深海カメラ筐体の造形に成功しました。
◇SLA方式とエポキシ樹脂を採用
深海カメラの回路基板をしっかりと支えつつ、レンズの精度を保てる筐体を作るには、精密な設計と工夫が必要です。R大学の研究チームは、カメラの安定性を確保するために、液体樹脂を注入しカメラのレンズを空中に浮かせることにしました。
筐体はSLA方式の3Dプリンターで作り、液体樹脂にはエポキシ樹脂を採用しました。SLA方式の造形物は弾性率に優れ、表面が滑らかでふたつのパーツを隙間なく結合することが可能です。
エポキシ樹脂は、液体のエポキシ樹脂と硬化剤から構成される液体樹脂で、耐久性と耐水性・防水性に優れています。研究チームはこの方法により、深海の圧力に耐えられる深海カメラ筐体を完成させています。
◇Form 3Lの特徴
研究チームが使用した3Dプリンターは、formlabsの業務用3DプリンターForm 3Lです。Form 3Lの主な特徴は、次のふたつです。
・2倍のレーザーパワーで速さと高精細の両立
最新のLFS(Low Force Stereolithography)テクノロジーを採用し、より正確で安定した造形が可能です。また、新たに2機のLPU(Light Processing Unit)が搭載されています。
これにより、250mWの2モジュールレーザー出力およびスポット径85ミクロンの精密で強力なレーザーで、サイズの大きな造形物でも、スピーディーに高精度で再現性の高い造形が実現できます。
XY解像度は25μm、レイヤー厚みは25 – 300μm、最大造形サイズは200mm × 335mm ×300mm(Form 3の5倍のビルドボリューム)です。
・無料専用ソフトウエアで管理も簡単
無料専用ソフトウエアを使用することで、3Dプリントの準備から管理まで一貫して行えます。完成されたエコシステムにより、ストレスのないスムーズな運用が可能です。専用ソフトウエアは操作性に優れているため、初心者も出力から後処理まで簡単に扱えます。
Form3Lで研究を促進
Form3Lの導入は、さらなる研究の促進にも役立ちます。R大学の研究チームも、深海カメラ筐体を完成させた後、光ファイバーケーブルの誘導や固定に使う器具や人工呼吸の部品の開発を成功させ、より高いレベルで社会貢献を果たしています。
◇他ツールも製作
深海カメラ筐体の成功により、3Dプリンターで造形した部品は、水中で十分使用できることが証明され、R大学の研究チームは他のツールの製作にも取り掛かりました。そのひとつが、光ファイバーケーブルの誘導や固定に使う器具です。
Form 3Lにより、サイズの小型化と高性能化もスムーズにできました。
◇プロトタイプ
新型コロナウイルス感染症が流行した際には、R大学の研究チームはForm3Lで人工呼吸器の部品のプロトタイプ(試作モデル)の製作にも挑戦しています。
研究チームのアイデアは医療機関の研究者からも関心を集め、共同研究が開始されました。その結果完成したのが、人工呼吸器の「Y字型スプリッター」に使われている部品です。
3Dプリンターによる造形は、採用する方式によって気密性が大きく異なります。特に、SLA方式やMJ方式は他の方式に比べて非常に高い気密性を持ち、水中で使用される部品の製作に最適です。
一方で、3Dプリンターで水中使用の部品を製作する際の最大の課題は、高い耐久性と防水性を確保することです。海中では圧力が増すため、造形時に生じるわずかな隙間からも海水が侵入するリスクがあります。
このため、部品が強い圧力に耐えられるように、適切な材料と造形方法の選定が不可欠です。さらに、防水性を高めるために含浸処理や塗装も施されますが、完全な防水性を達成するのは容易ではありません。
R大学の研究チームは、深海の高圧環境に耐えるカメラ筐体を製作するため、SLA方式の3Dプリンターとエポキシ樹脂を組み合わせることに成功しました。エポキシ樹脂は耐久性と防水性に優れており、SLA方式の精密な造形技術と相まって、深海でも使用可能な高性能な筐体が完成しました。
このプロジェクトで使用されたのは、formlabsの業務用3DプリンターForm 3Lで、最新のLFS(Low Force Stereolithography)テクノロジーと2機の高精度レーザーを搭載しています。これにより、サイズが大きくても精度の高い造形物がスピーディーに作成可能で、研究の効率が大幅に向上しました。
さらに、この成功を踏まえ、R大学のチームは光ファイバーケーブルの誘導・固定器具や、人工呼吸器の部品の試作モデルも製作しました。これらのツールは、高度な医療研究にも応用され、人工呼吸器の「Y字型スプリッター」の部品として実用化されました。このように、3Dプリンター技術の進化は、深海研究から医療分野まで、幅広い分野での革新と社会貢献を可能にしています。
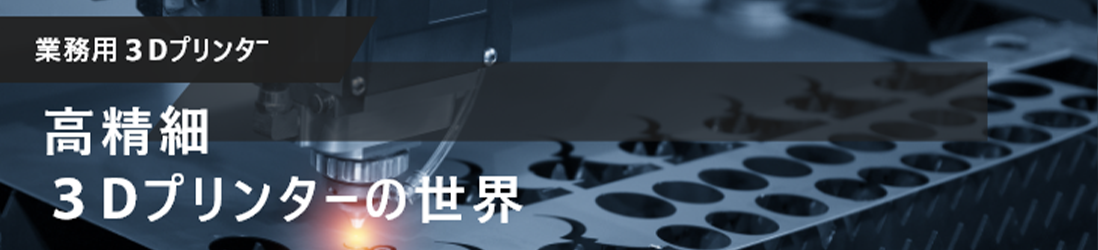